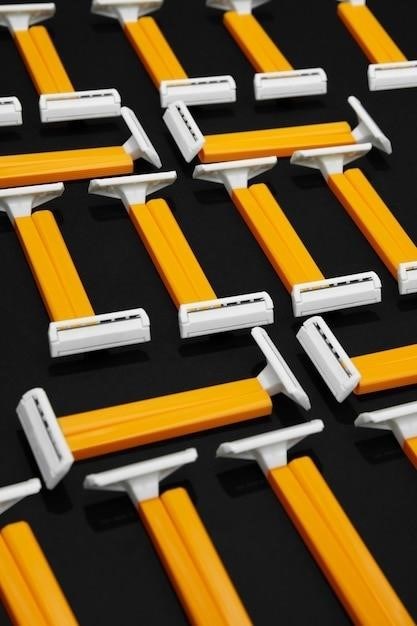
Compounding HDPE with Six Sigma
This article explores the application of Six Sigma principles to enhance the compounding of High-Density Polyethylene (HDPE). It examines the benefits of Six Sigma in manufacturing, specifically focusing on HDPE, and how these principles can be used to optimize the compounding process. The article includes a case study on reducing HDPE bag damage, demonstrating the practical application of Six Sigma in this context. It also delves into the Lean Six Sigma methodology, the DMAIC approach, and the financial metrics used to assess the success of Six Sigma projects.
Introduction to Six Sigma
Six Sigma is a data-driven methodology aimed at improving the quality of products, processes, and services by identifying and eliminating defects and minimizing variability. It originated in manufacturing but has since expanded its reach to diverse sectors, including healthcare, finance, and supply chains. The core principle of Six Sigma is to achieve near-perfection by reducing defects to a rate of 3.4 defects per million opportunities. This translates to a level of quality that is exceptionally high and significantly reduces waste and inefficiencies.
Six Sigma employs a structured approach that involves defining, measuring, analyzing, improving, and controlling (DMAIC) key business processes. This systematic framework allows organizations to identify and address root causes of defects, optimize processes, and achieve sustained improvements. The methodology emphasizes a data-driven approach, relying on statistical analysis and rigorous measurement to ensure objective decision-making. This data-driven focus helps eliminate subjective biases and ensures that improvement efforts are grounded in factual evidence.
The key to Six Sigma’s success lies in its ability to empower teams to take ownership of process improvement. This collaborative approach encourages cross-functional teams to work together, share knowledge, and identify solutions. By fostering a culture of continuous improvement, Six Sigma promotes innovation and a commitment to excellence throughout the organization. The methodology also prioritizes the use of specialized tools and techniques to streamline processes and enhance efficiency. These tools include statistical process control (SPC), failure mode and effects analysis (FMEA), and design of experiments (DOE), which are employed to identify and address potential problems, optimize process parameters, and ensure consistent quality.
Six Sigma in Manufacturing
Six Sigma has profoundly impacted the manufacturing landscape, revolutionizing how companies approach quality control and process optimization. Its adoption has been particularly impactful in industries where consistency and precision are paramount, such as automotive, aerospace, and electronics. Six Sigma’s application in manufacturing focuses on identifying and eliminating defects that arise during the production process, thereby enhancing product quality, reducing rework, and minimizing waste.
One of the key benefits of implementing Six Sigma in manufacturing is the significant reduction in production costs. By minimizing defects and rework, Six Sigma helps companies streamline their production processes, leading to increased efficiency and lower operational expenses. This cost reduction can also be achieved by optimizing resource utilization, minimizing downtime, and improving overall productivity. Moreover, Six Sigma empowers manufacturers to improve customer satisfaction by delivering products that meet or exceed expectations. By reducing defects and ensuring consistent quality, Six Sigma helps build trust and loyalty among customers, contributing to brand reputation and market share.
Six Sigma’s influence extends beyond the production floor, positively impacting supply chain management, product development, and customer service. By improving communication and collaboration across departments, Six Sigma fosters a culture of continuous improvement that benefits the entire organization. Its data-driven approach ensures that improvement efforts are grounded in objective evidence, leading to more effective and sustainable results. In a competitive global marketplace, Six Sigma provides manufacturers with a powerful tool to enhance their competitiveness, improve their bottom line, and achieve sustainable success.
HDPE in Manufacturing
High-density polyethylene (HDPE) stands as a versatile and widely used thermoplastic material in the manufacturing sector, renowned for its excellent properties, including high strength, rigidity, and chemical resistance. Its adaptability makes it a key player in various applications, including packaging, pipes, bottles, and even furniture. In the realm of packaging, HDPE’s durability and low permeability to moisture and gases make it ideal for storing food, beverages, and other consumer goods. Its resistance to chemicals and solvents makes it a suitable choice for containers used in industrial settings.
The manufacturing process of HDPE typically involves extrusion, a technique where molten HDPE is forced through a die to create desired shapes; This process allows for the creation of diverse forms, from thin films to thick pipes, meeting the specific requirements of various industries. HDPE’s versatility extends to its recycling potential, contributing to sustainable practices. Its ability to be recycled and reused makes it an environmentally responsible choice for manufacturers seeking to minimize their environmental impact.
The compounding of HDPE is a crucial step in the manufacturing process, where additives are incorporated into the polymer to enhance its properties. These additives can include stabilizers, pigments, and fillers, modifying the material’s color, strength, and other characteristics. The compounding process is vital for tailoring HDPE to specific applications, ensuring its suitability for diverse end uses. The effectiveness of HDPE compounding is greatly enhanced by the application of Six Sigma principles, which enable manufacturers to optimize the process, minimize defects, and achieve desired outcomes.
Compounding HDPE
Compounding HDPE is a critical stage in the manufacturing process that involves incorporating various additives into the polymer to enhance its properties and tailor it to specific applications. This process is akin to creating a custom blend of ingredients to achieve a desired outcome, much like a chef carefully combining spices and herbs to enhance a dish’s flavor. The additives used in HDPE compounding play a crucial role in determining the final characteristics of the material.
Stabilizers are added to protect HDPE from degradation caused by factors such as heat, light, and oxygen. Pigments are used to impart specific colors to the material, allowing for diverse visual aesthetics. Fillers, such as carbon black or calcium carbonate, are incorporated to modify the material’s mechanical properties, increasing its stiffness, strength, or impact resistance. The compounding process is typically carried out in a twin-screw extruder, where the HDPE granules are mixed with the additives under controlled conditions.
The extruder’s rotating screws melt and homogenize the mixture, ensuring uniform distribution of the additives throughout the polymer. The compounding process is a delicate balance, as the precise amounts and types of additives used can significantly impact the final properties of the HDPE. Careful control over the compounding process is essential to produce consistent and high-quality HDPE materials that meet specific performance requirements. The application of Six Sigma principles can further optimize this process, minimizing variability and ensuring reliable outcomes.
Six Sigma and Compounding HDPE
The application of Six Sigma principles to HDPE compounding can significantly enhance the efficiency and quality of this critical manufacturing process. Six Sigma’s focus on identifying and eliminating sources of variation and defects aligns perfectly with the need for consistency and precision in HDPE compounding. By systematically analyzing and improving the compounding process, Six Sigma can help manufacturers achieve a number of key benefits.
One of the primary advantages of using Six Sigma in HDPE compounding is the reduction of defects and variability. This translates to a higher yield of high-quality HDPE material, minimizing waste and maximizing production efficiency. By identifying and addressing the root causes of defects, such as inconsistent additive distribution, temperature fluctuations, or equipment malfunction, Six Sigma helps manufacturers create a more robust and reliable compounding process.
Furthermore, Six Sigma’s focus on continuous improvement fosters a culture of innovation and optimization within the manufacturing environment. By continuously seeking ways to refine the compounding process, manufacturers can achieve incremental gains in efficiency, quality, and cost-effectiveness. This translates to improved product performance, increased customer satisfaction, and a stronger competitive edge in the market. The integration of Six Sigma principles into HDPE compounding provides a powerful framework for driving excellence and achieving sustainable success in this critical manufacturing process.
Case Study⁚ Reducing HDPE Bag Damage
A compelling illustration of Six Sigma’s effectiveness in HDPE manufacturing is the case study of reducing HDPE bag damage in the carbon black industry. This study addressed a significant problem⁚ damaged HDPE bags not only resulted in direct economic losses for manufacturers but also led to customer dissatisfaction and a decline in brand reputation. To tackle this issue, the study employed the DMAIC (Define, Measure, Analyze, Improve, Control) approach, a core element of Six Sigma methodology.
The DMAIC approach guided the team through a structured process of problem definition, data collection and analysis, root cause identification, solution implementation, and ongoing monitoring. Through this process, the team discovered that the primary cause of bag damage was excessive handling and mishandling during storage and transportation. The team implemented several improvements, including optimizing warehouse layout, introducing specialized handling equipment, and implementing employee training programs on proper bag handling techniques.
The results were remarkable⁚ a significant reduction in bag damage, leading to substantial cost savings, enhanced customer satisfaction, and a strengthened brand image. This case study demonstrates the transformative power of Six Sigma in addressing real-world problems within the HDPE manufacturing sector, illustrating its effectiveness in improving quality, efficiency, and customer experience.
Lean Six Sigma Principles
The principles of Lean Six Sigma are deeply intertwined, forming a powerful approach to process improvement. While Six Sigma focuses on eliminating defects and reducing variability, Lean emphasizes the elimination of waste in all forms. This waste can manifest in various ways, including overproduction, waiting time, unnecessary transportation, inventory buildup, defects, over-processing, and underutilized talent.
Lean Six Sigma combines these principles to create a comprehensive framework for achieving operational excellence. It emphasizes a data-driven approach, using statistical methods to identify and eliminate root causes of defects and waste. Lean Six Sigma tools, such as value stream mapping, 5S methodology, and Kaizen events, are employed to streamline processes, reduce waste, and improve efficiency. The core idea is to deliver maximum value to customers while minimizing waste and maximizing resource utilization.
The synergy between Lean and Six Sigma creates a powerful force for continuous improvement. By eliminating waste and reducing variation, Lean Six Sigma enables organizations to achieve significant cost savings, increase productivity, enhance quality, and improve customer satisfaction. This approach is particularly relevant in HDPE manufacturing, where optimizing processes and reducing waste can directly impact the overall efficiency and profitability of the operation.
The DMAIC Approach
The DMAIC approach, a structured problem-solving methodology, is a cornerstone of Six Sigma. It provides a systematic framework for improving processes and achieving desired outcomes. DMAIC stands for Define, Measure, Analyze, Improve, and Control. Each phase plays a crucial role in driving improvement.
The Define phase establishes the problem or opportunity for improvement. This involves clearly defining the project scope, identifying the process under scrutiny, and understanding the customer needs and expectations. The Measure phase focuses on collecting data and establishing a baseline for the process. This involves identifying critical process variables, determining the current level of performance, and selecting appropriate measurement tools.
The Analyze phase involves analyzing the collected data to understand the root causes of defects and inefficiencies. This phase employs various statistical tools and techniques, such as Pareto analysis, cause-and-effect diagrams, and process capability analysis. The Improve phase focuses on developing and implementing solutions to address the identified root causes. This involves brainstorming potential solutions, testing and validating them, and ultimately implementing the most effective solution.
The Control phase aims to sustain the improvements achieved through the DMAIC process. This involves establishing monitoring systems to track the performance of the improved process, developing control plans to prevent regressions, and ensuring that the new process remains sustainable. By following the DMAIC approach, organizations can systematically identify and address process issues, leading to significant improvements in quality, efficiency, and customer satisfaction.
Financial Metrics for Six Sigma Projects
Evaluating the financial impact of Six Sigma projects is crucial for demonstrating their value and securing ongoing support. Several key metrics are commonly employed to assess the financial benefits of Six Sigma initiatives. These metrics provide a quantifiable measure of the return on investment (ROI) and the overall financial impact of process improvements.
One commonly used metric is Return on Investment (ROI), which calculates the net profit generated from the project divided by the total investment. This metric helps determine the financial return achieved from the Six Sigma project. Another important metric is Return on Assets (ROA), which measures the profitability of a company’s assets. ROA reflects the efficiency with which a company utilizes its assets to generate profits.
Net Present Value (NPV) is a metric that calculates the present value of future cash flows from a project, taking into account the time value of money. A positive NPV indicates that the project is expected to generate a positive return, while a negative NPV suggests that the project may not be financially viable. Internal Rate of Return (IRR) is a metric that calculates the discount rate at which the NPV of a project equals zero. It represents the effective annual return on investment.
Payback Period is a metric that calculates the time it takes for a project to recoup its initial investment. A shorter payback period indicates a faster return on investment. These financial metrics provide a comprehensive assessment of the financial impact of Six Sigma projects, enabling organizations to make informed decisions about resource allocation and project prioritization.